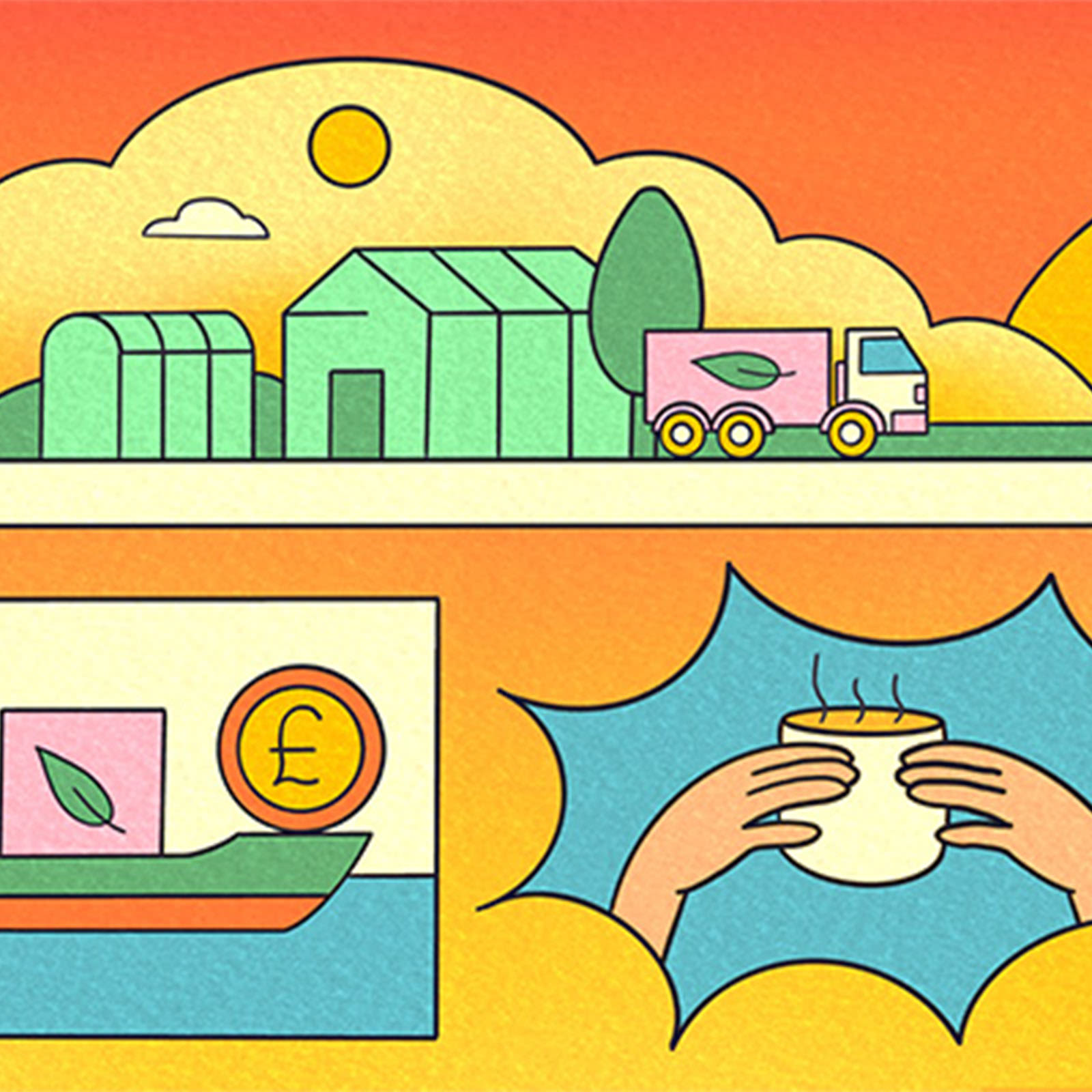
It's been a tough time managing supply chains in the past two years, as Covid, transit route closures (hello, Ever Given) and regulatory changes rock businesses' ability to do what they do best. That's not all, though: climate concerns and the environmental impact of transportation is also compelling companies to reassess where they source their raw ingredients and components. The result? Businesses are increasingly considering bringing part or all of their supply chains closer to home.
But reshoring (or even nearshoring) your operations can be a challenge. ‘Covid changed everything,’ says Ken Rosenblood, CEO and founder of ObVus Solutions, a manufacturer of ergonomic office equipment based in Los Angeles. Delays in getting his products from manufacturers compelled Ken to buy an 18,000 square foot building in Victor, New York, which would become his onshore manufacturing facility.
Obstacles and challenges
• It isn't cheap. Ken spent $4 million converting a former furniture store. But shipping container costs were skyrocketing and delays at ports meant he couldn't guarantee that those containers would even arrive on time. The cost of components in the US, Ken says, is also significantly more than in China. One of his products requires 38 different pieces. In China, those pieces cost $5; in the US, it was more like $25. To cut down on the costs, Ken thought laterally; he bought a CNC machine (a motorized manufacturing tool) and the raw materials and made the pieces himself.
• Nor is it easy. Ken advises those who plan to reshore their business to take the rule of three and double it to the rule of six: ‘You need to have a backup to your backup to your backup,’ he says. Nonetheless, reshoring manufacturing gives him more reliability and the opportunity to more quickly iterate on product prototypes – as well as an increased margin on those that make it to full production.
Take your time
Ken is far from alone in making the shift to reshoring (or nearshoring). Rob Bossen's paddleboard company, Grey Duck, had historically manufactured all of its products in China. In 2021, facing the same issues as ObVus Solutions, Rob collaborated with a Canada-based manufacturer on a line of new products. It worked well, so Grey Duck transformed its store in Minnesota into a manufacturing hub.
Rob still sources from China because of the range of products that his company offers. ‘To maintain that offering, we're going to have to continue to do some Asian manufacturing over the long term,’ he says. ‘But, likely, we'll just start to pick off some of our models and build them here.’ It wasn't simple and Rob advises building in double the amount of time you expect to manage reshoring or nearshoring your manufacturing. He also suggests easing your way in, rather than switching your manufacturing wholesale.
It's not an easy decision and it requires a leap of faith – but it can reap rewards. As for final advice, Ken's is simple: ‘Control what you can control, and hope for the friggin' best.’