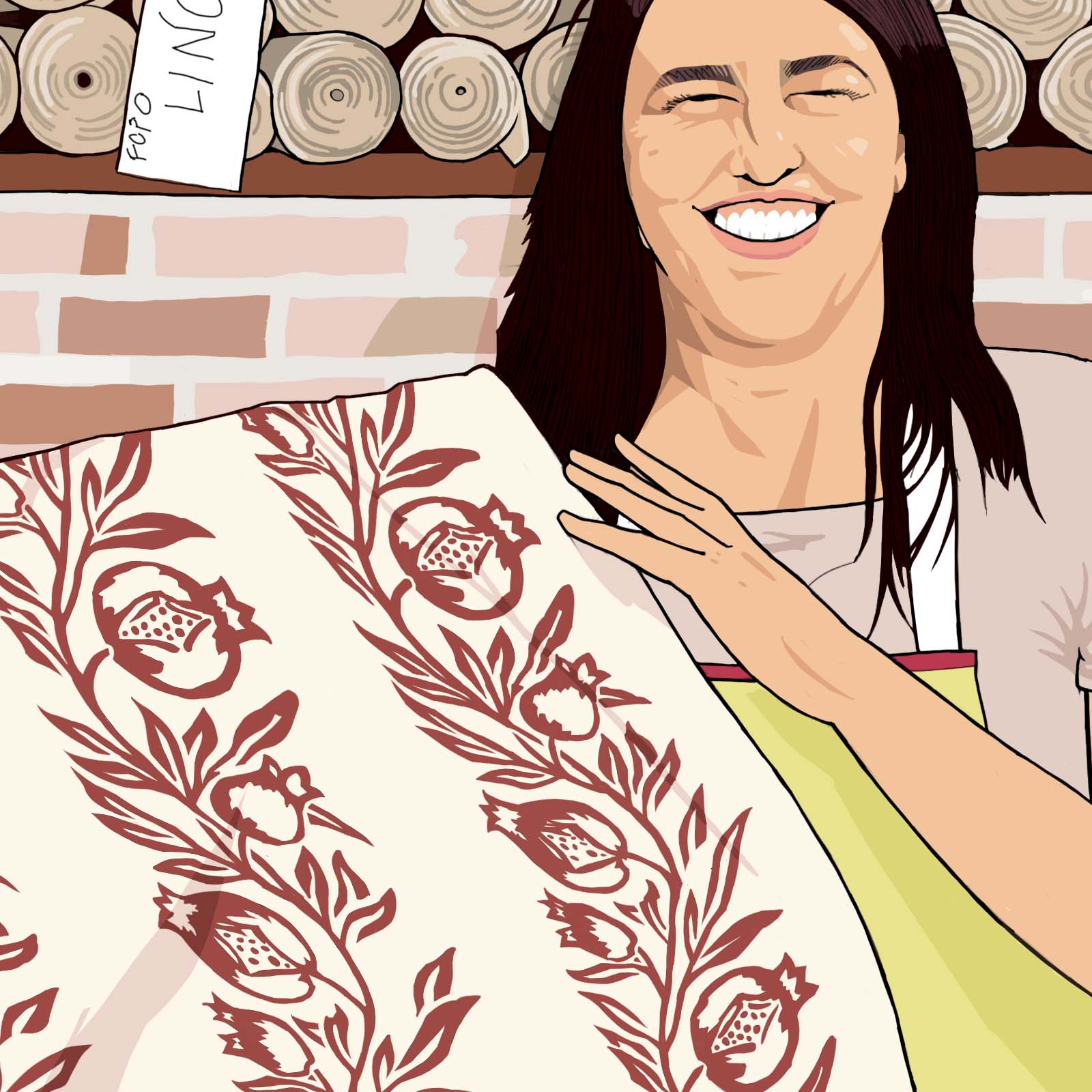
Beyond the bar buzzing with locals swigging espressos and a piazza that dates back to the Middle Ages, there's an industrial side to the otherwise quaint town of Fabriano in Italy. Tucked into a side street is a factory that's crafting show invites for some of the fashion industry's biggest brands.
This is no ordinary paper factory. Far from the glamor of Milan or Paris, Danila Versini, the co-founder of Manualis Cartiera, spends her days surrounded by soggy buckets of paper, stepping around puzzles and dodging enormous drying racks. Three men churn wet sheets of thick paper through what looks like a medieval torture device, pulling them out the other end and laying them out to dry. But no trees are harmed in the making of Manualis Cartiera's paper.
More like a lab than a factory, Manualis Cartiera uses centuries-old techniques to craft limited-edition runs of paper using waste materials, which range from the fabric off-cuts of huge fashion labels like Fendi and Armani to weirdly ingenious additions like human hair, coffee grounds and seeds. To bring it all full circle, Danila supplies the biggest fashion houses with packaging, show invites, luxury labels and more.
‘I came to paper-making as a game of chance,’ says Danila, who joined the industry after having her son, Leonardo. ‘I was trying to get back into the working game and I was never afraid to take a path less traveled so, when a friend told me that he was setting up a company in the paper sector and needed someone to market it, my journey in this world began.’ When the last paper factory they worked at closed in spring 2018, Danila and her partners Giacomo Arteconi and Andrea Clementi found themselves out of jobs. Five months later, Manualis Cartiera was born.
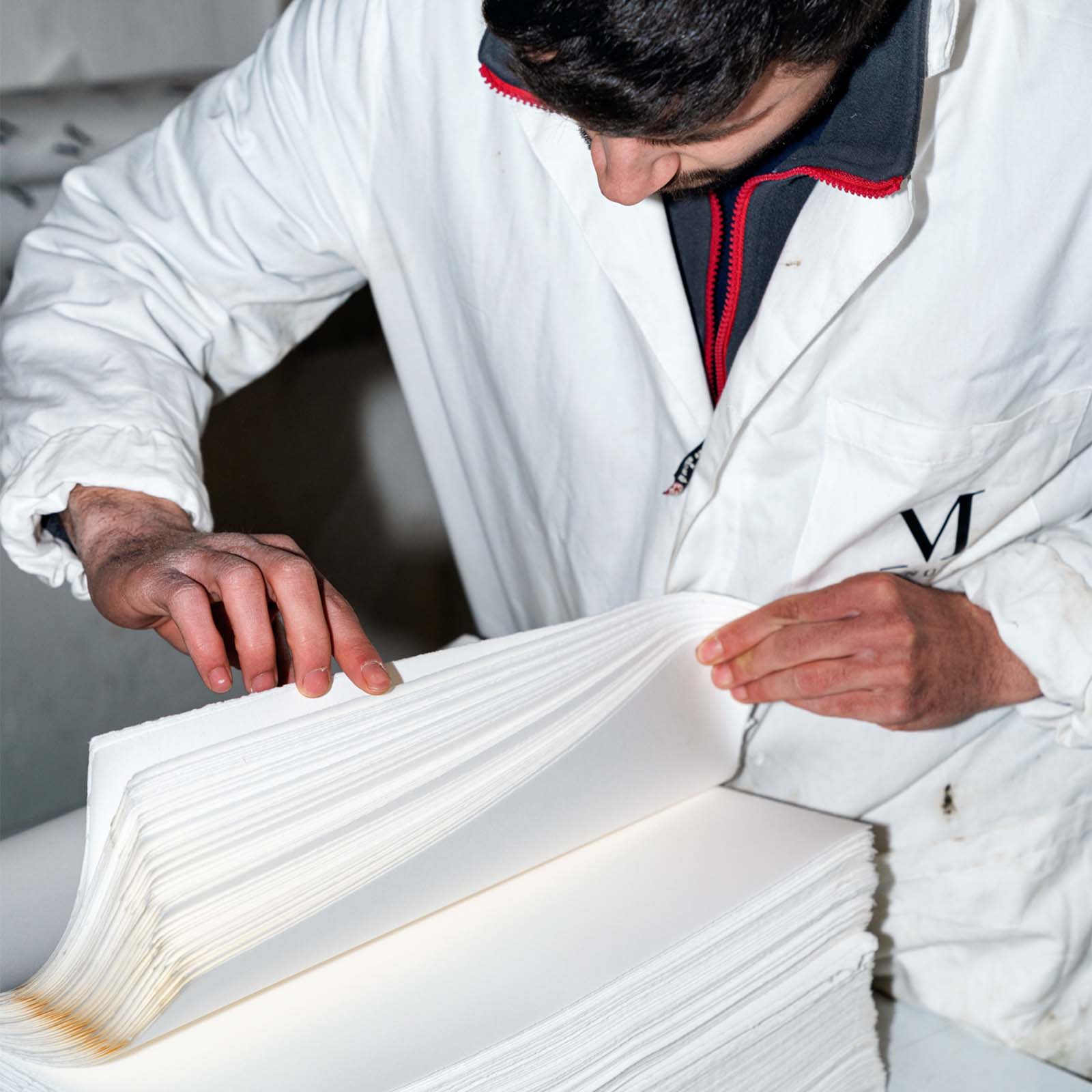
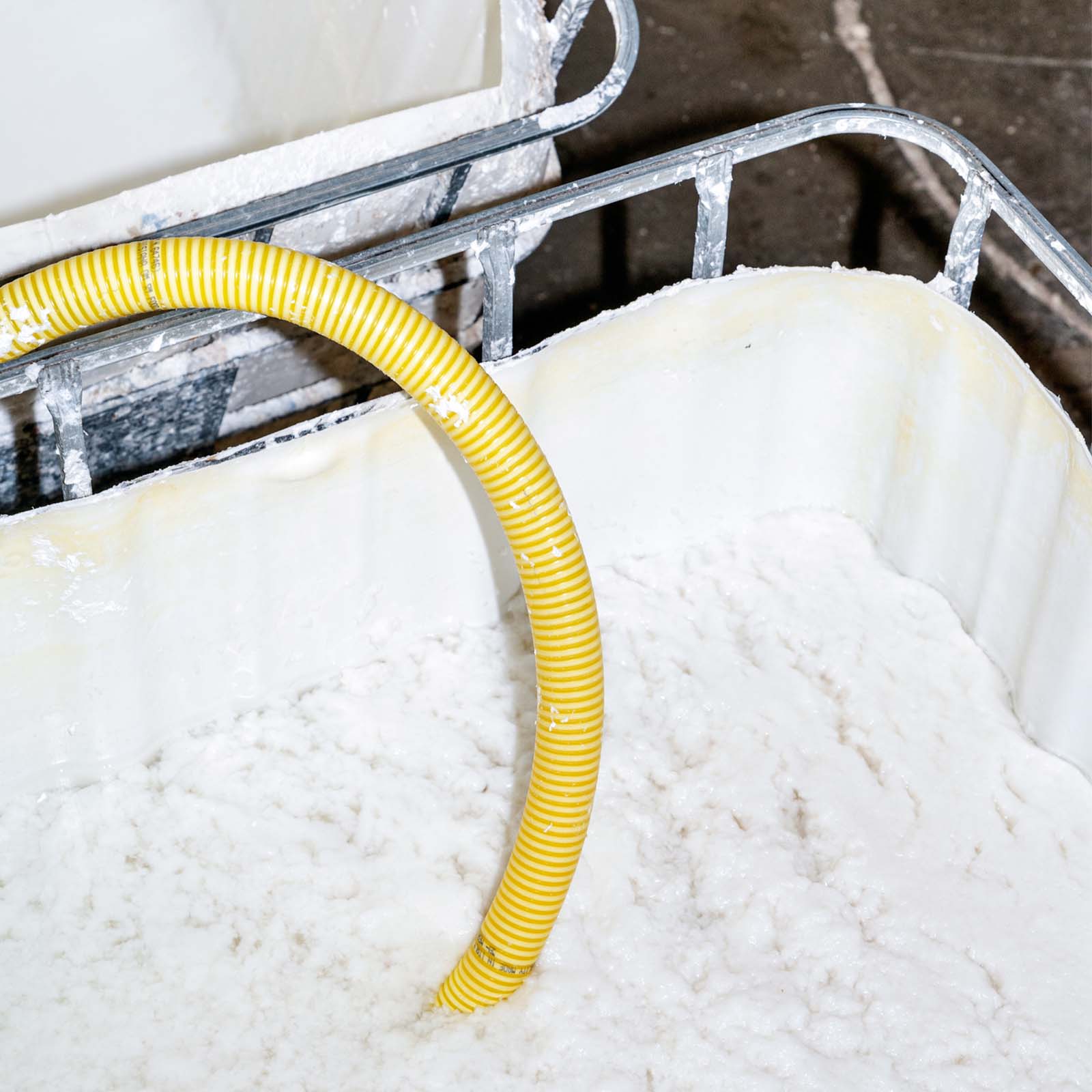
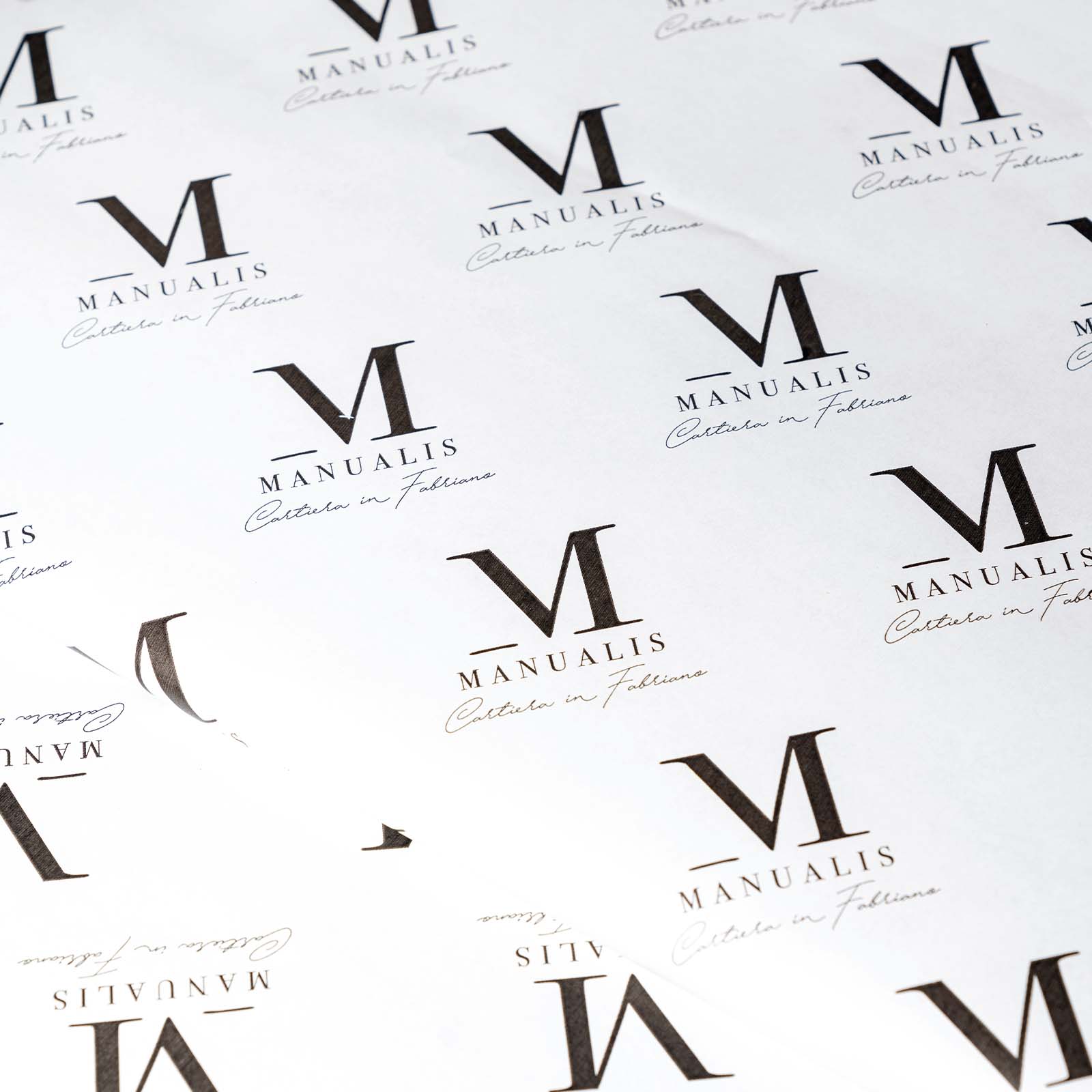
The history
‘We wanted to combine tradition and innovation by dressing these ancient skills of paper-making, which have characterized Fabriano for eight centuries, with new clothes,’ says Danila, peering into the great vats of liquid where cotton is being soaked, which will later be transformed by the lab into beautiful rectangles of art paper.
Paper-making arrived in Fabriano in the 13th century. The very first parchments in the town were made by combining cotton with animal gelatin, using weaving techniques inspired by wool looms to craft paper with visible laid lines when it was backlit. This wasn't your standard sheet of A4, but a thick, sturdy piece of textured paper that would take ink from a quill well. ‘Each master paper-maker was so proud of his work that he'd have an insignia stamped into the paper, so that whoever used or received that sheet would know that it was his,’ says Danila.
Ever since, the town has been known for its paper, with a famous art paper brand taking on the name of the town itself. But that isn't to be confused with the work Danila and her fellow artisans are doing at Manualis Cartiera. For one, the factory is less of a factory, but more a small laboratory. It deals with small-batch orders that are bespoke to each client and focuses on maintaining the ancient craft of paper-making, as opposed to resorting to industrial processes to churn out vast quantities.
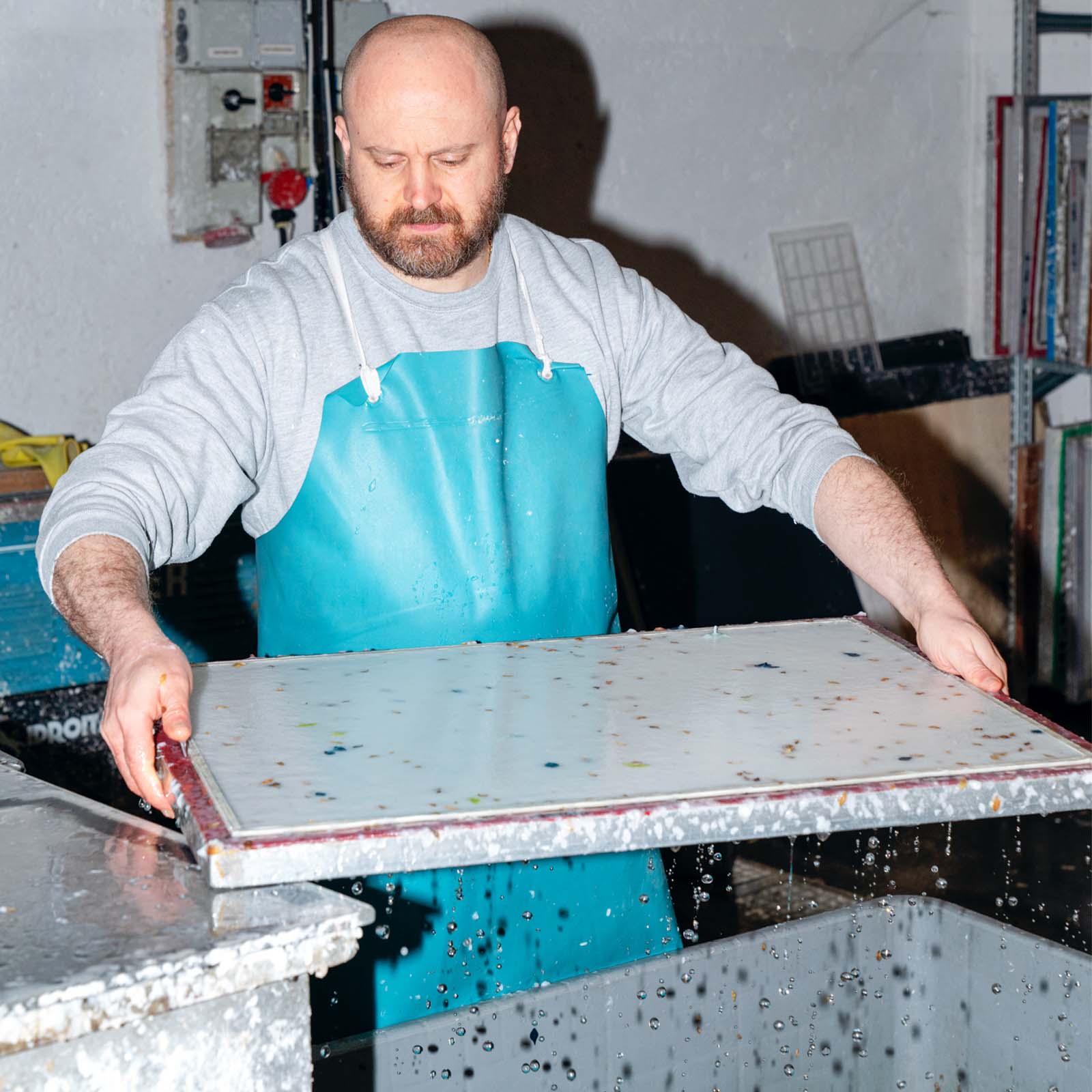
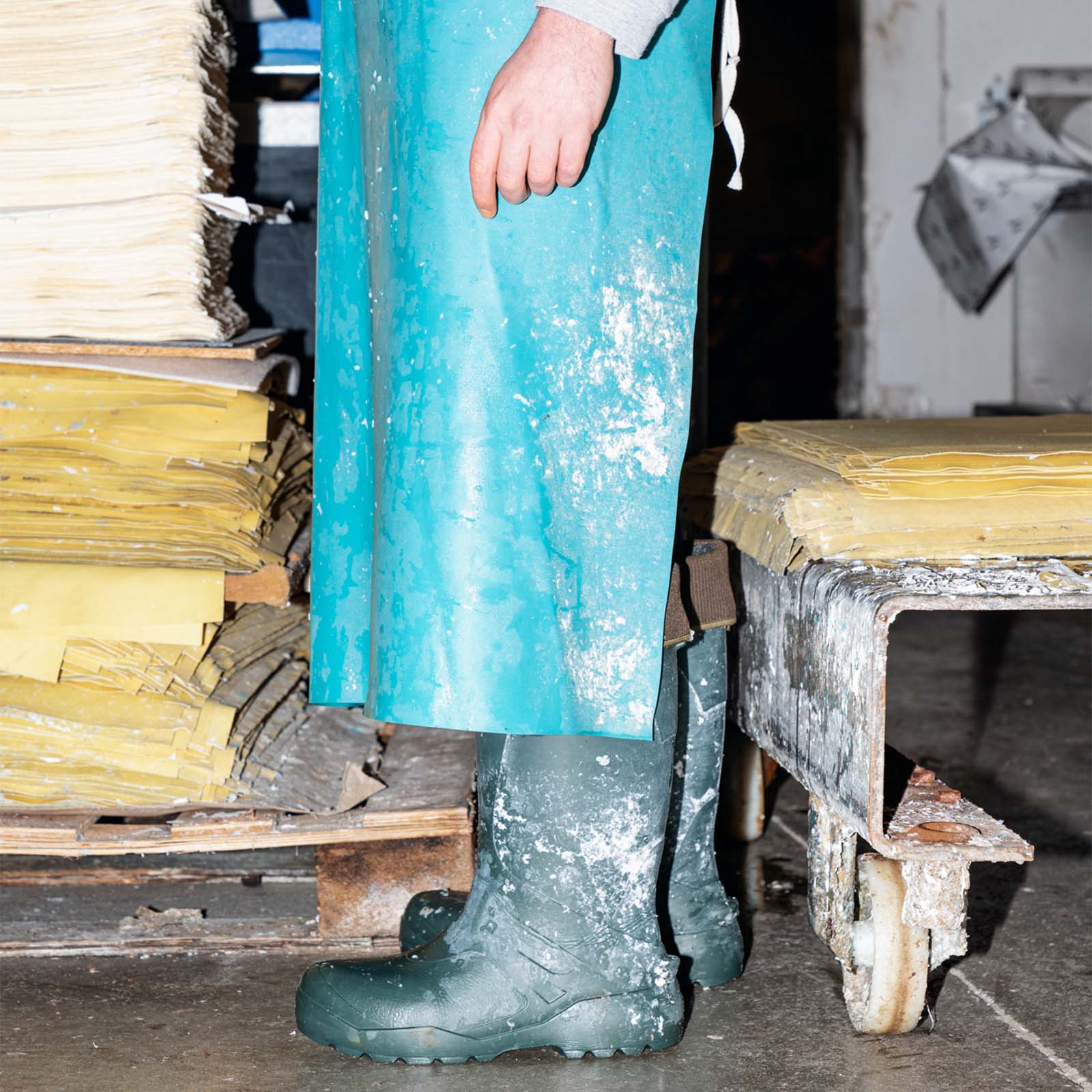
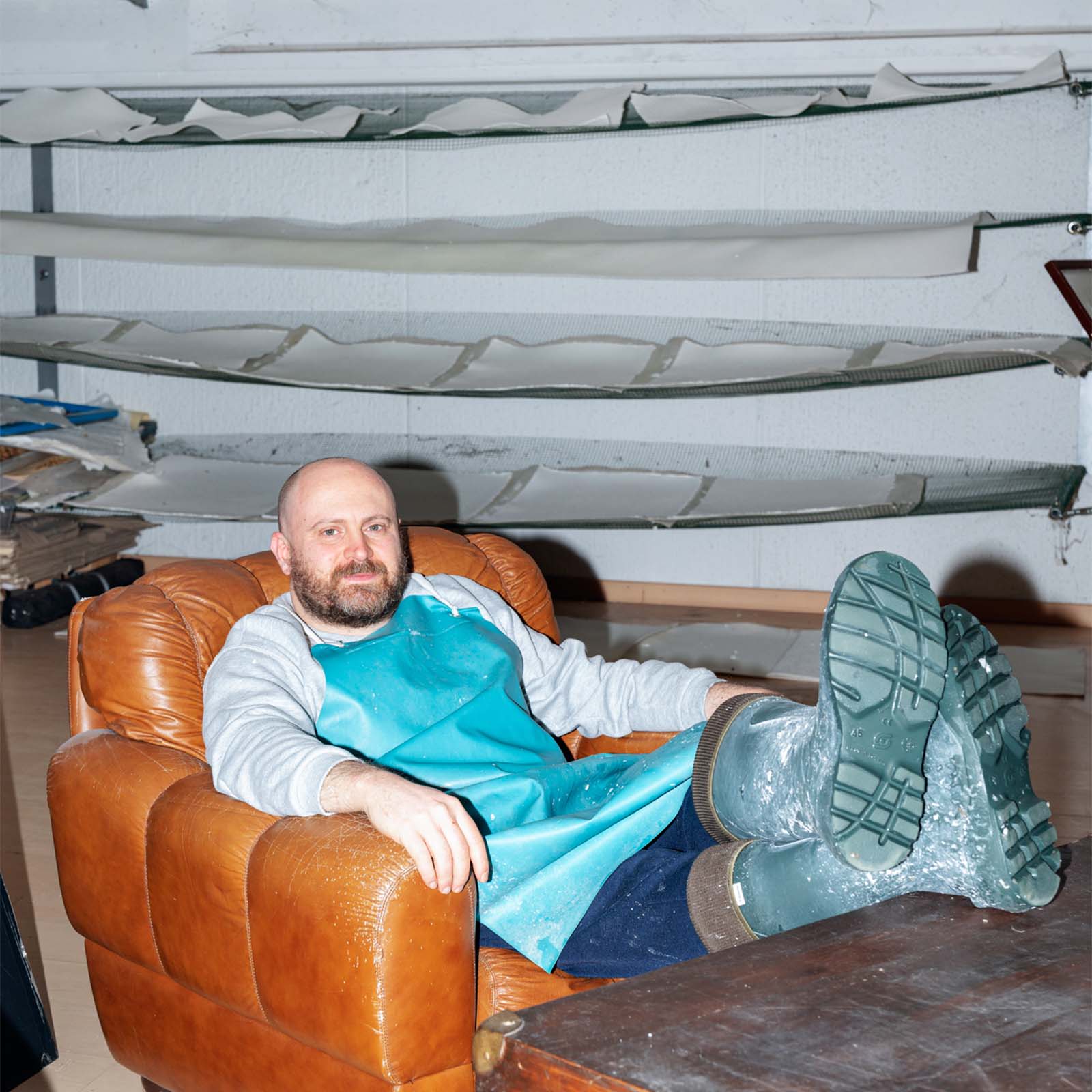
Nothing but natural
Unlike other factories that use cellulose from trees, Manualis Cartiera uses buds of cotton for its paper. Danila and her partners prefer to use fabric or other pulverized waste materials, mixed with a small amount of glue in vats of rainwater. They don't add chemicals and they still use the same process of hand-sifting their ingredients and weighing out how much of each mix they'll need for one sheet of paper.
Danila explains that instead of using machines that work at many meters per second, master paper-makers manually process and press each sheet of paper separately. We watch from a balcony as three men below sift out sodden, white liquid from a great vat of paper cotton mulch onto enormous trays. ‘They feel how much mix they need for each sheet and then press it themselves,’ she says.
The result is unique sheets of paper that can be made into fashion week show invites, capsule-collection packaging and distinct paper for discerning artists. Manualis Cartiera can produce only 400 sheets of paper per day, but each of those sheets is individual to the last.
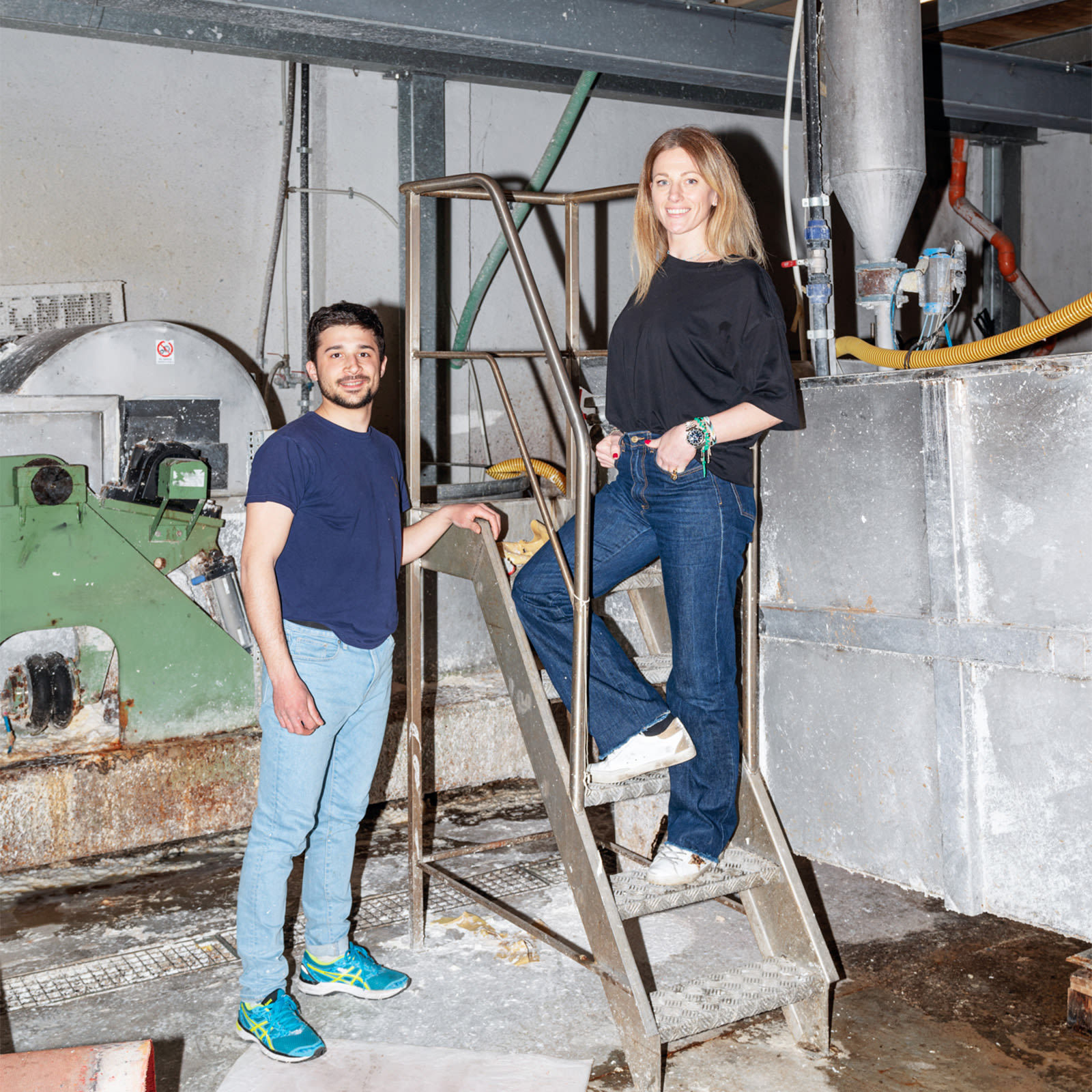
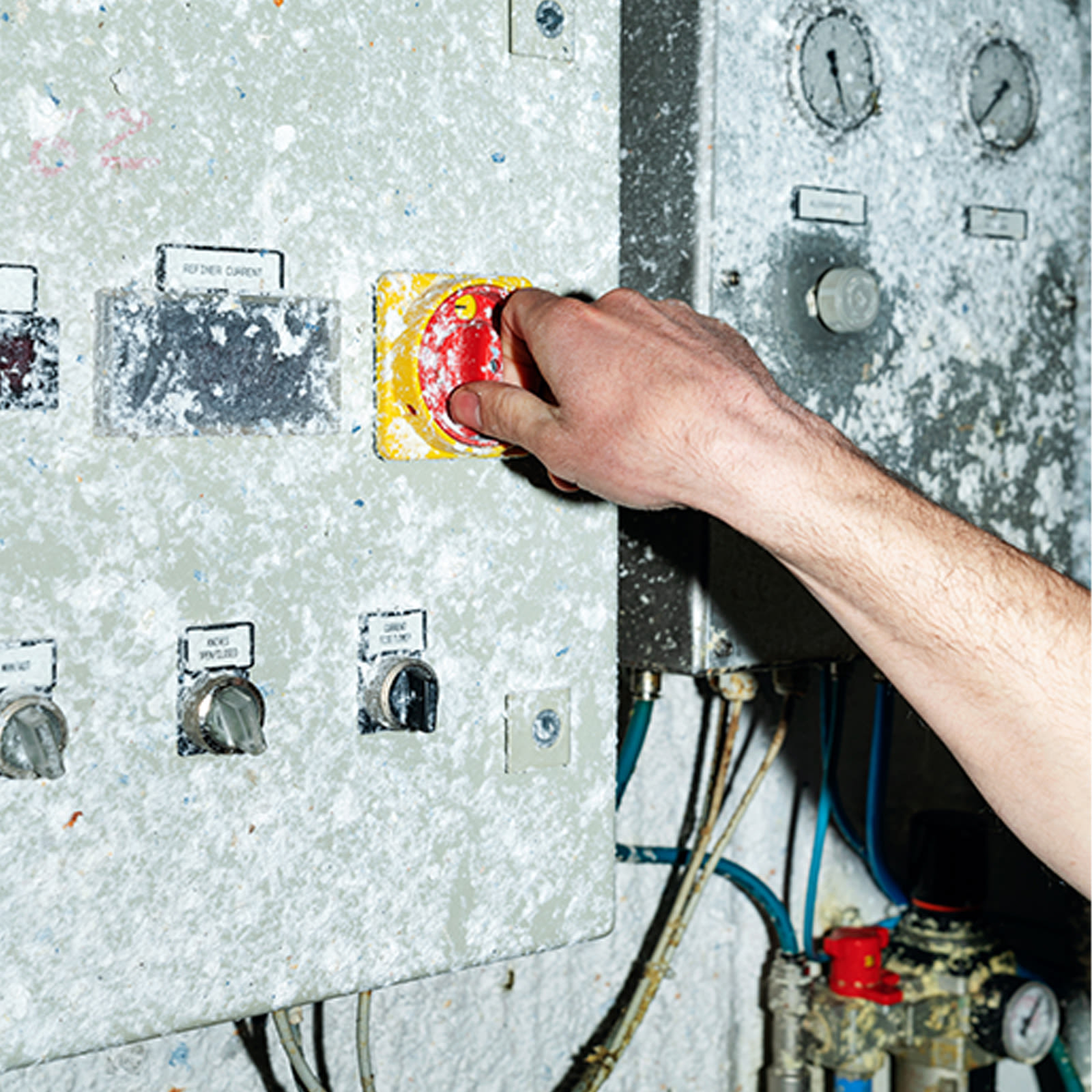
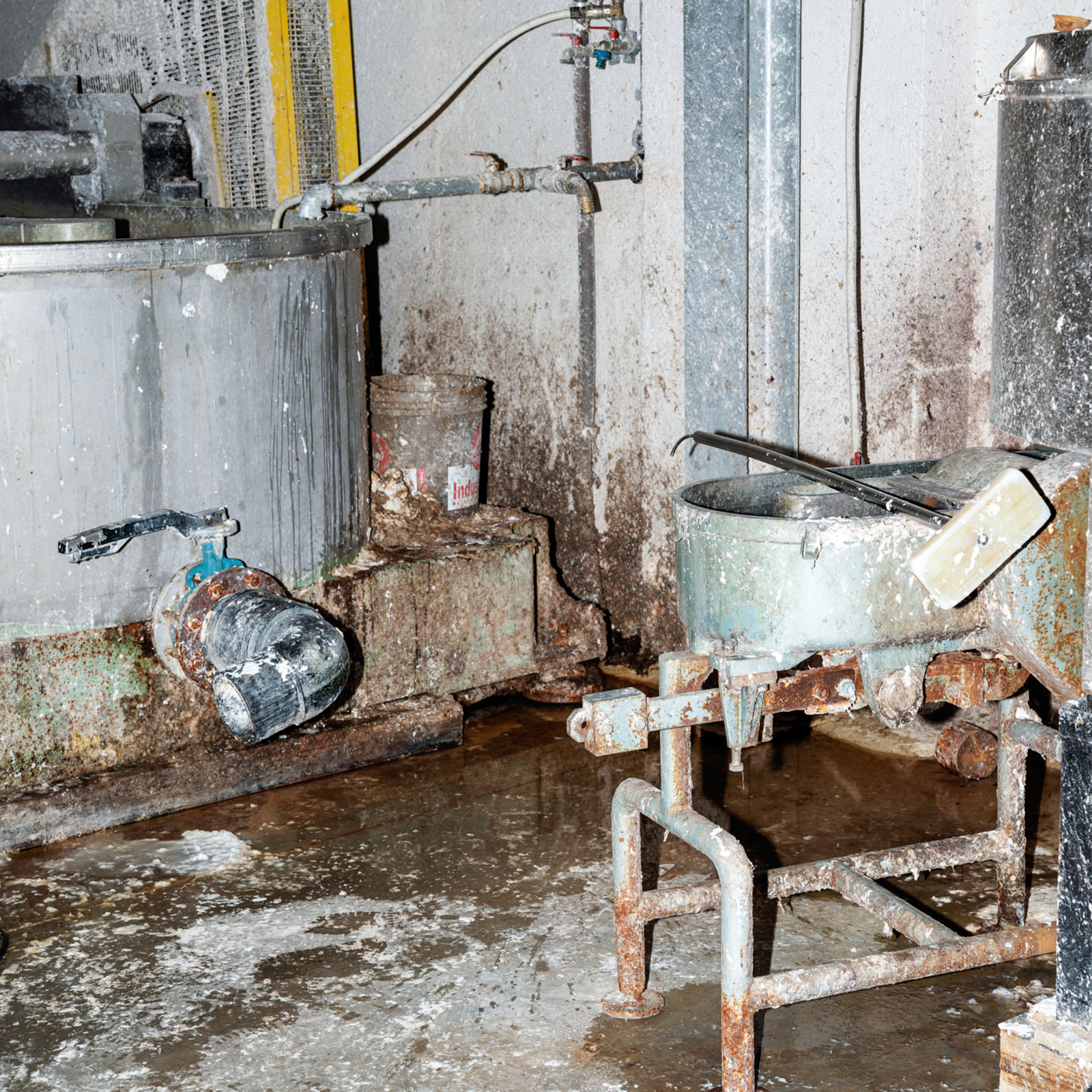
Collaboration is key
‘We've always focused on customization here,’ says Danila, handing over various sheets of paper and listing the components that make up each: denim, for a denim brand; cashmere off-cuts from a leading fashion house so big that they've asked her to sign a non-disclosure agreement, so as not to have their secrets and suppliers revealed. An A1 sheet of green-tinted paper is revealed to be hemp, while another blue sheet has been made from old lanyards. The strangest is a paper box for a wig brand, made from human hair.
‘The customers come to us as if [they've] entered the tailor's shop. They have the possibility to personalize their paper according to their needs and to their specific business,’ says Danila, who emphasizes that one of the most important focuses for Manualis Cartiera is a circular economy. A favorite project was plantable paper for the Zegna menswear label. Seeds for flowers were pressed into the fabric of the paper, so that when planted and watered, the paper would eventually bloom.
‘Magic happens with that textile or food waste that the customer provides us with,’ says Danila, smiling. ‘It's no longer rubbish but the very fabric of the paper. It gives a second life to a product destined for the bin.’ At Manualis Cartiera, recycled paper takes on a far more interesting meaning.
A version of this article was first published in Courier issue 47, June/July 2022. To purchase the issue or become a subscriber, head to our webshop.