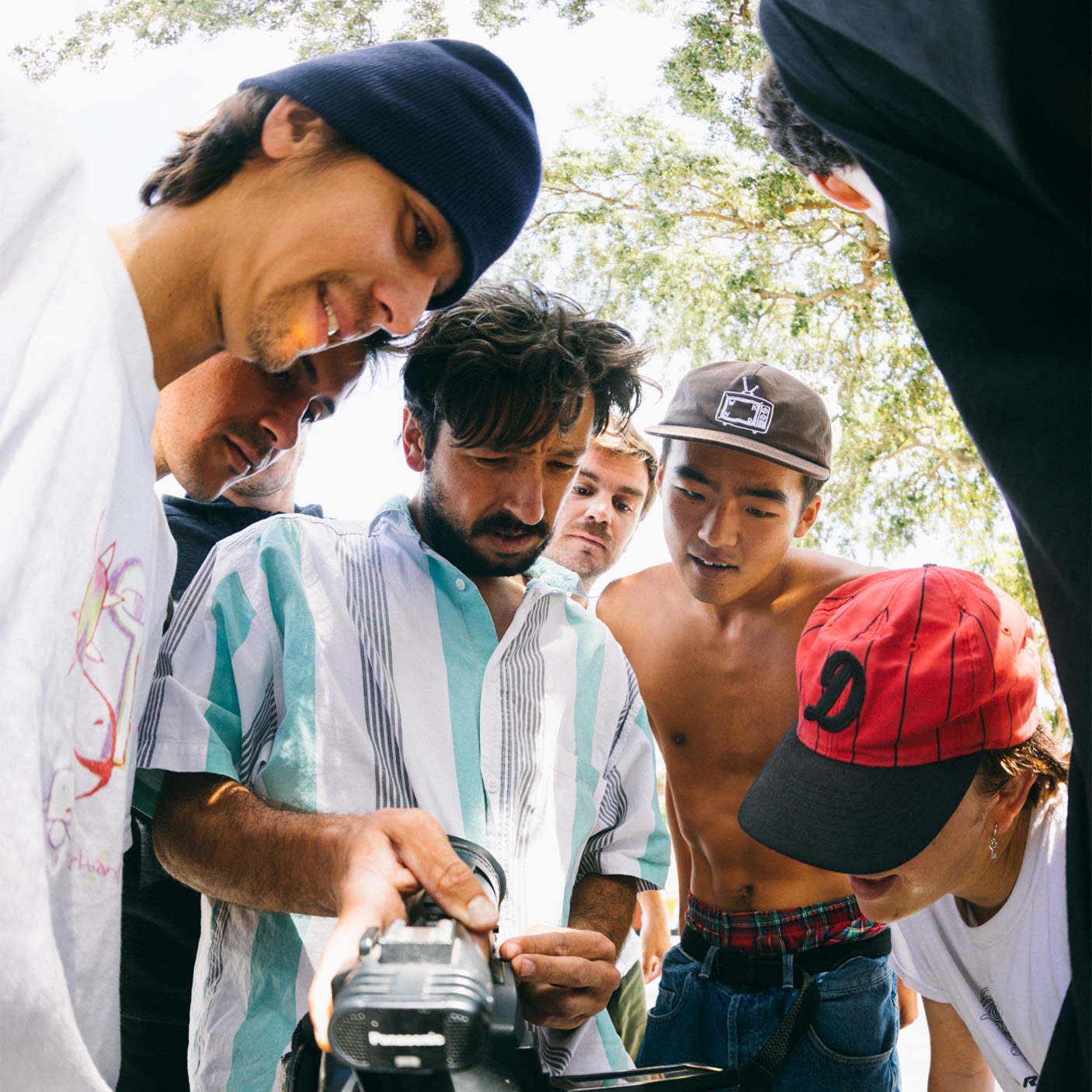
Courier’s Daniel Giacopelli caught up with Kodj Glover for the Courier Weekly podcast to explore how he went about setting up manufacturing processes for his own brand, Fuji&Hakone.
Listen to the clip above or read the story below. For the whole episode, click here.
‘I didn't mean to go to Alibaba, but I was looking for a loopwheel machine or a loopwheel manufacturer, which is referred to as Tsuriami-ki in Japanese. I was kind of putting all these phrase words and just plugging them into Alibaba. And then lo and behold, one popped up and I was like: oh shit, OK, wait, I can actually put an order in. This is crazy. Like, what? So I started off just with a T-shirt and some hoodies and I got them blank. I just had them sent over blank from Japan and then did all the screen print and all the appliqué badge stuff that I wanted to do here in the UK. But, of course that process is one, quite unethical. There's a lot of miles in there, there's a lot of stuff that I wanted to cut down on…’
What's unethical?
‘Just having it shipped from Japan to here from here to ship it to the screen printers and to do all the bits to have it shipped back to me.’
So the carbon footprint was too big?
‘It was just something in the back of my head that was niggling me, like: you need to make this process a lot easier. And there was only one way I thought I could do that, was going to Japan. I just had to go and see someone. I had to go and put some faces to names.
‘So I get there, I'm like, cool, I'm here. What day is good? Booked in a day. They sent me the location. It took me hours to try and find it. This is in Osaka, me and my girlfriend. And then we get there and literally you'd think I was like Versace or something. They were so happy to see me that I was like you don't even understand. I'm crying inside.’
Was this because Japanese people are just so hospitable? Or they didn't know who you were…
‘No, I don't think they knew or gave a damn who I was. I just think they were impressed that I was actually here in the physical. I think a lot of people get to a point in starting a clothing company and then the price hits or reality hits and you're almost like: shit, OK, maybe let me come back to that. They were like, ‘This young boy’ – I don't know if they remembered my Central Saint Martins story or not, but they're thinking this young man from fashion school – ‘we've been speaking to him for three years and he's here.’ Like what? So they gave me the grand tour. I saw everyone. I shook everyone's hand. It was a surreal experience…’
Red carpet…
‘Do you know what I mean? It'd be great if I could say that when I came back from Japan it was smooth sailing, but it definitely wasn't. It was 18 months of getting design files in the right format. Because I'm sending them PNGs and stuff and for a while it's OK, but then you need to start sending screens and your line sheets and everything. So. yeah, it was a lot of back and forth.
‘Long story short, we kind of got all the files over, things were nice and smooth, but two things happened. One was by the time I was ready to order because they produced the garments on this slow machine, the loopwheel machine, which is like 10 times slower than a normal machine now to produce garments. I mean, they produce a fraction of your high-speed machines. So that meant by the time I wanted to order, they had no XLs, they had all these odd numbers of stock. And I was just like: OK, first hurdle. But I took it anyway. The second was they went forward and produced all the garments before I officially signed off, or I had cost per unit. So as you can imagine, all my estimations and my prices were just all made up. And when I did get the reality of the cost per unit… Oh shit. I had to refactor and rethink a lot of stuff because, you know, made in Japan, this process, it all starts to add up.’
Click here for more episodes of the Courier Weekly.